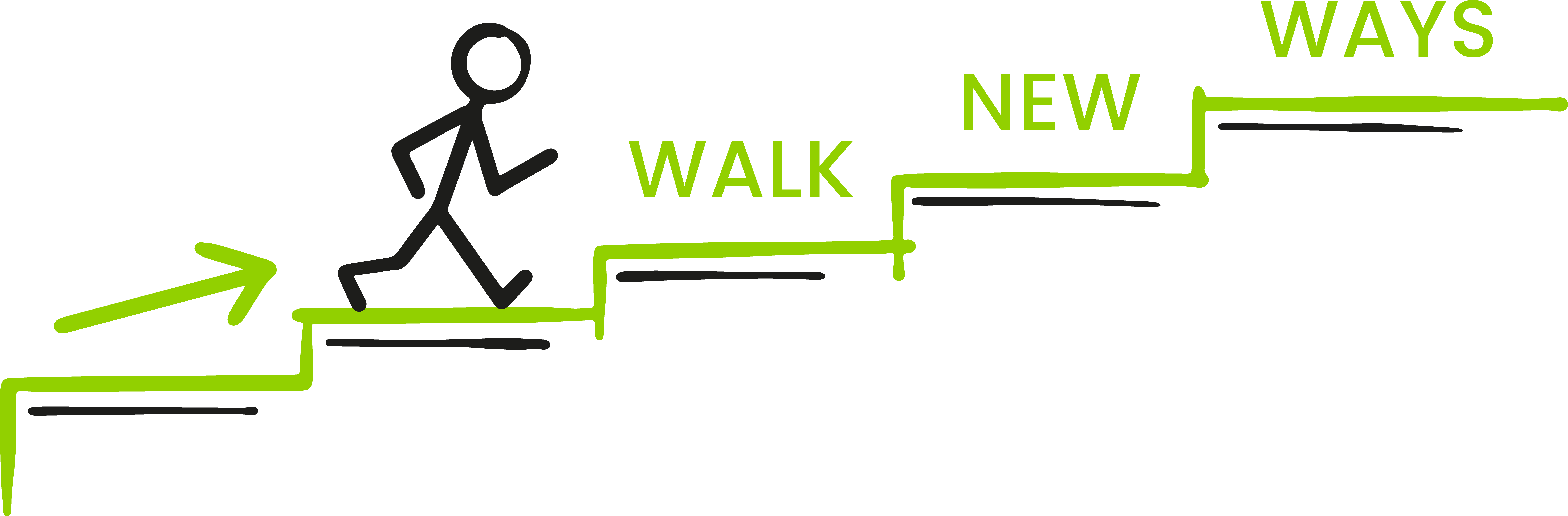
Was ist 3D-Druck und wie funktioniert das?
Der umgangssprachliche Begriff 3D-Druck wird heute als Additive Fertigung bezeichnet und ist das Gegenteil zu den subtraktiven Verfahren. Bei subtraktiven Verfahren wird von einem kompakten Materialblock mittels Fräsen, Drehen oder Bohren Material abgetragen und so zu einem Bauteil geformt. Die Additive Fertigung ist im Gegensatz dazu ein materialauftragendes Verfahren, bei dem das Bauteil frei von geometrischen Einschränkungen schichtweise aufgebaut wird.
Wo liegen die Vorteile des 3D-Drucks?
Zu den konventionellen Herstellungsverfahren bietet der 3D-Druck Vorteile in mehreren Hinsichten:
- Geringer Zeit- und Materialaufwand
- Form- und Funktionsoptimierung
- Individuelle Produkte
- Geometrisch aufwendige und komplexe Bauteile
- Ohne zusätzliches Werkzeug
- Innenliegende komplexe Strukturen wie z.B. Kanäle, dünnwandige oder lose Teile
Gerade im Bereich der Kleinserien- und Prototypenproduktion sehen wir hier das ideale Verfahren im 3D-Druck.
Das geht auch mit Keramik?
Keramische Bauteile lassen sich ebenfalls mittels 3D-Druck herstellen. Der stereolithografische 3D-Druck (kurz STL) war die erste Technologie welche keramische Bauteile herstellte, die in der Industrie als Hochleistungskeramik Anwendung fanden. Mit der STL-Technologie lassen sich dünnwandige, hochkomplexe und nahezu formfreie Keramikbauteile herstellen.
Neu und revolutionär sind die Verfahren, welche wir zur industriellen Herstellung von dünn- bis dickwandigen und komplexen Keramikbauteilen einsetzen. Wir setzen auf das Laser-Induzierte-Schlickerguss-Verfahren (kurz LIS) und das Lagenweise-Schlicker-Depositions-Verfahren (kurz LSD). Mit der Erweiterung um diese beiden Druckprozesse werden die Grenzen in der Produktion von keramischen Bauteilen neu gesteckt.
Warum brauchen wir 3D-Druck in der Keramik?
Die Herstellungsprozesse bzw. -verfahren in der Keramik haben sich in den letzten hundert Jahren nicht geändert. Es gibt im Grunde nur vier industrielle Formgebungsverfahren, das Pressen aus Pulver oder Granulaten, das Extrudieren aus plastischen Massen sowie der Schlicker- und Spritzguss aus keramischen Suspensionen. Alle Verfahren benötigen für jedes neue Bauteil ein angepasstes Formgebungswerkzeug. Diese sind sehr teuer und in den meisten Fällen erst ab einer Stückzahl von mehr als 10.000 Bauteilen ökonomisch. Damit sind sie für die Herstellung von Prototypen oder Kleinserien nicht geeignet. Des Weiteren ist die Bauteilkomplexität mit den konventionellen Verfahren eingeschränkt. Gerade in der heutigen Zeit steigt die Anforderung an die Bauteilkomplexität und -formflexibilität immer stärker an, weil die zugehörigen Produkte immer kleiner und leichter werden sollen. Dadurch ist die Industrie auf neue Formgebungsverfahren angewiesen. Der 3D-Druck ist in der Lage diese Lücke zu schließen.
Und wo liegt der Unterschied zwischen LIS und LSD?
Mit beiden Verfahren lassen sich schnell und unkompliziert dichte, dickwandige keramischen Bauteile erzeugen und das ganze unabhängig von Material und dessen Partikelgrößen. Dies wird durch die Verarbeitung von wasserbasierten und nahezu organikfreien Suspensionen ermöglicht. Grundsätzlich ist zu sagen, dass LSD für eine höhere Auflösung und Detailgenauigkeit steht. LIS ist jedoch für die schnelle Herstellung von einzelnen mittelgroßen Prototypen mit hoher Wandstärke ideal.
Schaut Euch die technologischen Unterschiede der Verfahren im Detail auf den zugehörigen Unterseiten an: